5 Ways Digital Twin Technology Can Improve Manufacturing Efficiency
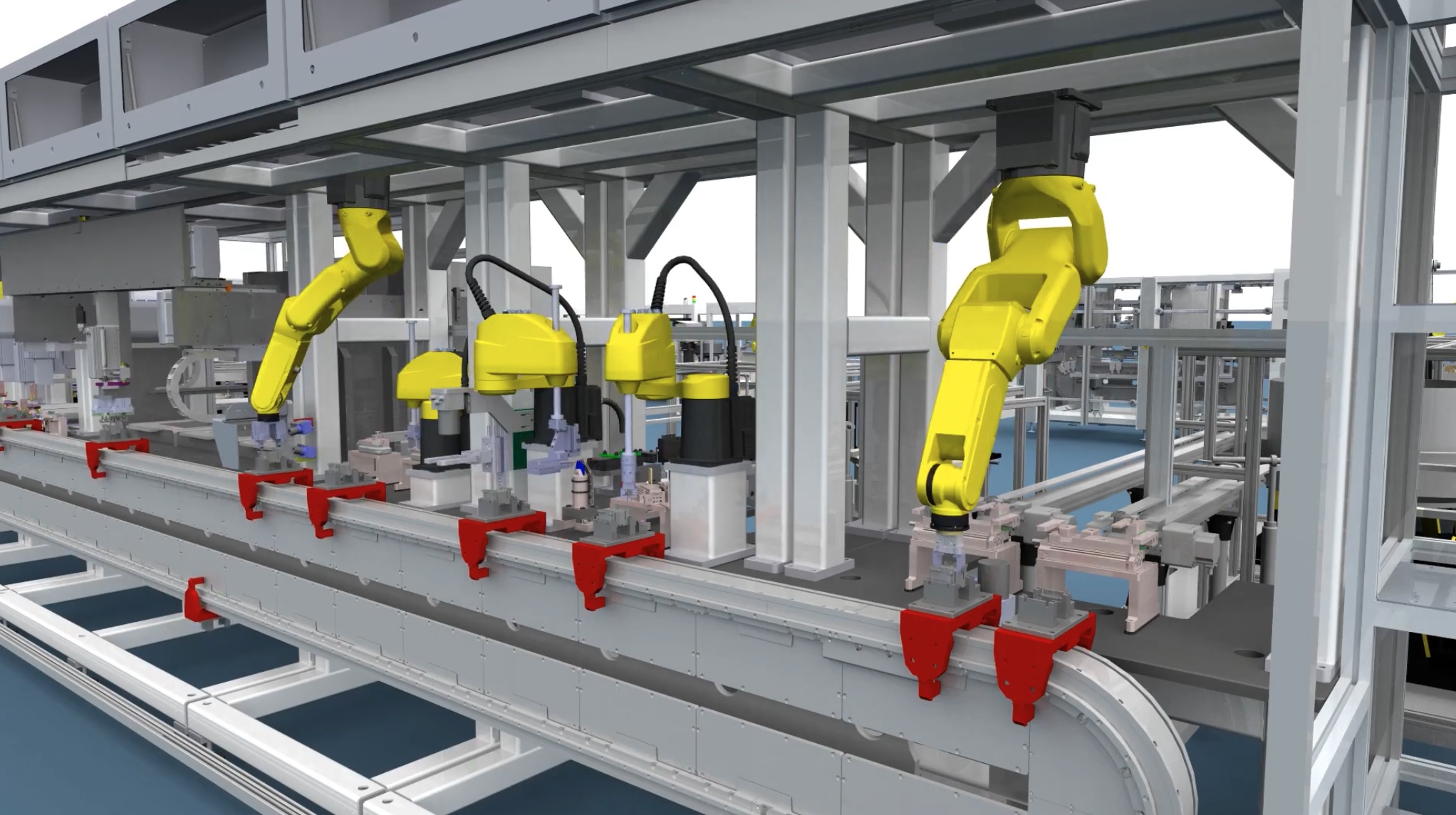
Efficiency is vital in the manufacturing industry, as it enables businesses to streamline operations, minimize waste, and maximize profits while maintaining high product quality and competitive pricing. One tool manufacturers can utilize to analyze and implement more effective processes and systems is a digital twin – a virtual replica of manufacturing operations.
By leveraging a digital twin, businesses can simulate real-world scenarios, analyze performance, and identify opportunities for improvement without disrupting day-to-day operations. From optimizing scheduling to maximizing labor utilization, there are several ways digital twin models can streamline processes, drive innovation, and boost overall performance.
Here are five examples of how Automation Intelligence has helped our clients utilize digital twin technology to improve their businesses:
1. Optimizing scheduling
If your Manufacturing Execution System (MES)—or worse, manual spreadsheets—is handling production order assignments, it’s likely relying on inefficient planning heuristics. Our decision science team leverages digital twin technology and mathematical optimization to create precise, data-driven schedules that maximize production efficiency while minimizing costs.
2. Debottlenecking material movements
End-of-line controls logic, which ensures sellable products exit the system, can often become a bottleneck. Our simulation team can replicate these problematic system behaviors in a digital twin, enabling us to develop targeted logic improvements that enhance flow and increase throughput.
3. Reducing changeovers and downtime
Scheduling is key to ensuring changeovers occur only when necessary. A digital twin can not only optimize the changeover schedule but also serve as a virtual reality training environment for operators. VR allows operators to practice in a realistic setting, working together to safely, efficiently, and quickly retool machines for the next production run. This hands-on training ensures a smoother transition and enhances overall production efficiency.
4. Methods for maximizing labor utilization
Simulating people in virtual environments provides a data-driven approach to understanding workforce utilization. By modeling workflows and identifying inefficiencies, businesses can test innovative strategies, optimize task assignments, minimize downtime, and ensure that employees are deployed in the most effective way possible.
5. Safely improving raw material inventory
Many large facilities incur holding costs for raw materials before they’re converted into sellable products. We can help determine optimal holding levels that minimize excess costs while ensuring productive assets aren’t at risk of stockouts.
Maximizing Impact Through Tested Improvements
These are just a few of the common opportunities we've observed in practice. Continuous improvement professionals have a deep understanding of their processes, and we collaborate with them to test and validate any improvement plans before implementation. Before making any changes, it's crucial to ensure that the change delivers measurable benefits and doesn't introduce unforeseen issues elsewhere in the system.
How could digital twin technology improve your business?
If you're ready to explore how digital twins can transform your business, reach out to the Automation Intelligence team. We're here to help you unlock new efficiencies and elevate your manufacturing practices to the next level.
Headquarters
We have a team of engineers positioned across the US, but our primary HQ is in Atlanta, GA.